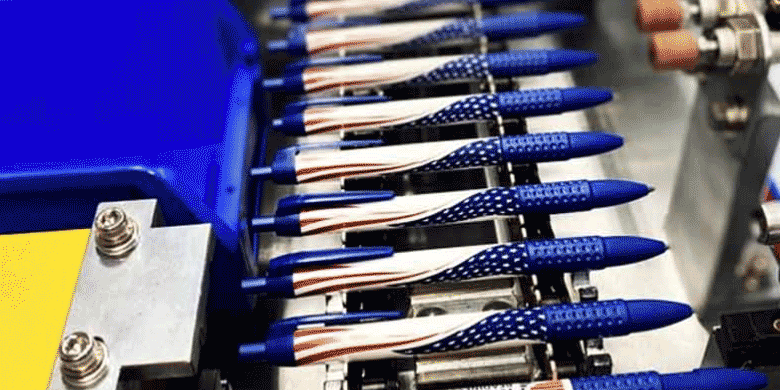
9 April, 2024
Pen Factories: An Inside Look at How Different Pens are Manufactured
In a world where digital devices are increasingly dominating, a pen remains a steadfast tool in our daily lives. Whether scribbling notes, doodling, or signing important documents, they are indispensable. But have you ever wondered how these writing instruments are made? Let's take a fascinating journey into pen factories to discover the art and science behind the manufacturing of traditional pens.
The Pen: A Brief History
Before diving into the manufacturing process, it's worth noting how pens have evolved. From quills dipped in inkwells to fountain pens and the modern ballpoint, the journey of pen development is a testament to human ingenuity. Today, the most common types are ballpoints, rollerballs, and fountain pens, each with its unique manufacturing process.
The Ballpoint Pen: A Manufacturing Marvel

In the realm of writing instruments, the ballpoint pen stands out as a marvel of modern manufacturing. Its ubiquity belies the complexity and ingenuity behind its design and production. This article delves into the technical aspects of how ballpoint pens are made, covering everything from the choice of materials to the intricate assembly process.
1. Design and Materials
A) Materials
- Plastic and Metal Varieties: Promotional ballpoint pens are commonly made from plastics like polystyrene, polypropylene, and ABS (Acrylonitrile Butadiene Styrene). Higher-end pens may incorporate metals such as brass, aluminium, or stainless steel. The choice of material impacts the pen’s weight, durability, and cost.
- Considerations for Material Selection: Factors influencing material choice include the intended market segment (luxury, commercial, educational), manufacturing costs, and the pen’s functional requirements.
B) Design Phase
- Aesthetic and Functional Design: The design phase is critical, where the pen’s look, feel, and functionality are conceptualised. This involves ergonomic considerations to ensure comfort during use and aesthetic aspects like shape, colour, and texture.
- Technical Specifications: Designers also focus on technical details, such as the pen's length, diameter, and the type of ink refill it will accommodate. The design must ensure a seamless user experience, from the ease of writing to the pen's longevity.
2. Manufacturing Process
A) Body Production
- Injection Molding Process: The pen’s body and cap are typically produced using injection moulding. This involves melting plastic granules and injecting them into a mould under high pressure. This mould is precisely crafted to the pen’s specifications.
- Cooling and Ejection: Once the plastic is injected, it cools and solidifies within the mould, taking the shape of the pen's body and cap. The parts are then ejected from the mould.
B) Ink Preparation
- Formulation of Ink: The ink in ballpoint pens is a critical component. It is a viscous oil-based formula, comprising a mixture of dyes for colour, solvents to maintain fluidity, and lubricants to facilitate smooth writing.
- Colour Variations: The ink formulation is adjusted for different colours and types of pens. The viscosity and drying time are carefully calibrated to ensure consistent writing quality.
3. Assembly of the Tip
- Tip and Ball Assembly: The tip, often called the nib, is where the tiny ball sits. This ball is usually made of materials like tungsten carbide or stainless steel.
- Mechanism of Action: The ball fits snugly in a socket, with enough freedom to roll as the pen moves across the paper. As it rolls, it picks up ink from the cartridge and dispenses it evenly on the writing surface.
4. Fitting the Refill
- Inserting the Ink Refill: The refill – a thin tube filled with ink – is inserted into the pen’s body. In retractable pens, a spring mechanism is included to retract and extend the tip.
- Ensuring Compatibility: The refill must be compatible with the pen’s design, ensuring that it seats correctly and that the ink flows consistently to the tip.
5. Quality Checks
- Rigorous Testing: Each pen undergoes extensive quality checks. These include tests for ink flow, to ensure it is consistent and doesn’t skip; durability tests, to ensure the pen withstands regular use; and functionality tests, like click or twist mechanisms in retractable pens.
- Final Inspections: The pens are also visually inspected for any manufacturing defects, ensuring that only pens meeting high-quality standards reach the consumer.
Manufacturing ballpoint pens is a fine balance of engineering, design, and precision. Each step is crucial in creating a reliable and efficient writing tool, from the choice of materials to the intricate assembly of the tip and ink system. The next time you pick one up, consider the meticulous processes behind its creation – a testament to the fusion of industrial manufacturing and design innovation.
The Rollerball Pen: Precision in Every Line
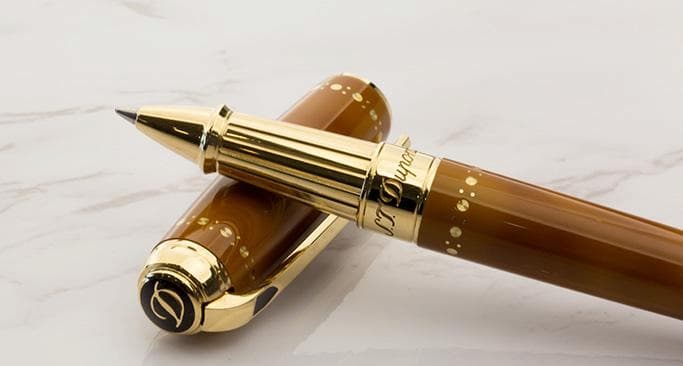
Rollerball pens are renowned for their smooth and precise writing experience, distinguishing themselves from their ballpoint counterparts. The secret behind their performance lies in their unique construction and ink formulation. Some of the technical aspects of how rollerball pens are manufactured are below, where we focus on their distinctive tips and ink and the intricate assembly process.
1. The Tip and Ink Difference
A) Liquid Ink
- Water-Based or Gel Ink: Rollerball pens use ink that is either water-based or gel-based. This type of ink is less viscous than the oil-based ink used in ballpoints, allowing for a smoother flow onto the paper.
- Ink Formulation: The formulation involves a careful balance of pigments, water (or gel), and other solvents. This composition ensures that the ink flows freely but also dries quickly on paper to prevent smudging.
B) Fine Tip
- Precision Manufacturing: The tip of a rollerball pen, which houses a small ball bearing, is made with high precision. The ball, typically made from stainless steel or other hard materials, needs to be perfectly spherical and smooth.
- Ink Delivery System: The challenge in manufacturing the tips lies in ensuring a consistent ink flow. The tip’s design must precisely control the ink release while the ball rotates, allowing for fine, consistent lines without leaking or botching.
- Quality of Materials: Given the fluidity of the ink, the materials used in the tip assembly must be resistant to corrosion and wear, ensuring longevity and consistent performance.
2. Assembly Process
A) Similarities to Ballpoints
- Staged Assembly: Like ballpoints, they are assembled in stages. This process typically includes the preparation of the pen’s body, the fitting of the ink reservoir, and the assembly of the tip and cap.
- Component Integration: Each component must integrate seamlessly with the others, ensuring that the overall pen is balanced, comfortable to hold, and easy to use.
B) Attention to Ink Delivery
- Preventing Leaks: One of the critical focuses during their assembly is preventing ink leaks. This involves ensuring airtight seals between the ink reservoir and the tip.
- Testing for Smooth Writing: Each one is tested for its writing capabilities. Tests include checking for a smooth and uninterrupted ink flow, ensuring the pen writes immediately upon contact with the paper, and verifying that the ink does not skip or bleed excessively.
- Quality Control: Given the pen's reliance on a fluid ink system, rigorous quality control is vital. This includes checking the integrity of the ink chamber, testing the durability of the tip, and ensuring the pen's overall reliability.
The manufacturing of rollerball pens is a fascinating blend of precision engineering and careful craftsmanship. From the finely-tuned tip designed for flawless ink flow to sophisticated ink formulations, every aspect is crafted to provide an unparalleled writing experience. As you glide one across a page, remember the intricate processes and meticulous attention to detail that went into creating such a precise and enjoyable writing tool.
The Fountain Pen: An Elegance in Writing
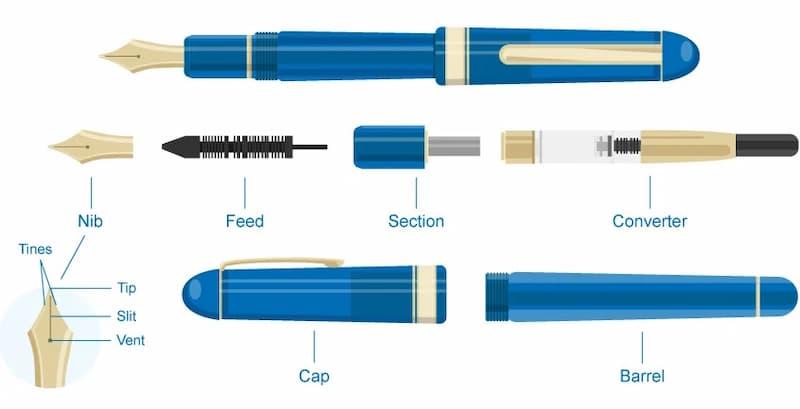
Fountain pens are not just writing instruments; they are a blend of artistry and engineering, symbolising elegance and sophistication in writing. The creation of a fountain pen involves skilled craftsmanship and a deep understanding of the intricate mechanics behind its operation. The detailed process of making a fountain pen highlighting the craftsmanship involved in nib crafting, the selection of materials for the body and reservoir, and the meticulous assembly process are described below
1. Craftsmanship and Materials
A) Nib Crafting
- Material Selection: The nib, which is the heart of a fountain pen, is usually made from precious metals like gold and silver for their flexibility and corrosion resistance. Stainless steel is also a popular choice for its durability and resistance to wear.
- Precision Crafting: Crafting a nib is a fine art. It involves precise shaping and cutting to create the perfect point. The nib must have the right degree of flexibility to provide a smooth writing experience, adapting to different writing pressures and styles.
Customisation: They often offer customised nibs, tailored to the writing characteristics of the individual, such as angle, pressure, and line width preferences.
B) Body and Reservoir
- Diverse Materials: The body of a fountain pen can be crafted from a variety of materials, ranging from durable plastics to luxurious metals and even precious materials like ivory or mother-of-pearl.
- Ink Reservoir: The ink reservoir, a critical component, can be a refillable cartridge or a built-in piston mechanism. This requires precise assembly to ensure a leak-proof and efficient ink flow.
- Design and Aesthetics: The design of the body is often as important as its functionality. It involves considering the aesthetics, weight, and balance of the pen, ensuring it is comfortable to hold and use.
2. The Art of Assembly
Hand Assembly
A) Personal Touch: Many are assembled by hand, reflecting their status as luxury items. Hand assembly allows for careful attention to detail and ensures that each pen meets high standards of quality.
- Skilled Artisans: The assembly is often carried out by skilled artisans who have honed their craft, understanding the nuances of pen mechanics and aesthetics.
3. Quality and Testing
- Ink Flow Testing: A critical aspect of the testing process is ensuring consistent and smooth ink flow. The pen must deliver ink to the nib in a controlled manner, allowing for a seamless writing experience.
- Nib Smoothness: The nib undergoes rigorous testing to ensure it glides smoothly across the paper without scratching or skipping.
- Balance and Comfort: The overall balance and comfort in the hand are also tested. A well-balanced one reduces hand fatigue and enhances the writing experience.
The creation of a fountain pen is a meticulous process that combines traditional craftsmanship with modern engineering. From the precision crafting of the nib to the careful assembly of the body and reservoir, each fountain pen is a testament to the artistry and skill involved in its making. These pens are not just tools for writing; they are works of art that offer a timeless elegance and a unique writing experience. In a world increasingly dominated by digital technology, it stands out as a symbol of refinement and personal expression.
The Wrap
The manufacturing of traditional pens is a blend of modern technology and age-old craftsmanship. In pen factories around the world, the focus is on precision, quality, and reliability. Despite the rise of digital technology, the demand for traditional pens remains strong, highlighting their enduring appeal and functionality. So, the next time you pick up a pen to write, take a moment to appreciate the intricate process behind its creation.
The Pens Only Team